So, I've got this old truck bed trailer which I've had for many years. I believe it was a ford, but don't exactly remember as the bed was in bad shape and I tore it off and scrapped it years ago. I've decided to make it into a welding trailer to consolidate my equipment and make it portable when I need to work on something outside the barn. It would definitely live over 90% of its life in the barn. Since it's only the frame, axles, etc, I am letting my imagination run pretty wild with what I want to do with it. For starters, I'm thinking of just building a large flatbed to mount everything to. The current dimensions I'm toying with is about 10' long x 80" wide. This width would cover the wheels and negate the need to construct new wheel wells. Some other design thoughts are as follows:
- Leave a fairly large area on the back free for use as a welding table. The height seems very good but will change as the design proceeds.
- Build legs on large casters at the 4 corners to make it a table. The trailer wheels to be off the ground in this configuration.
- Transform the tongue to make it removable so it would truly be a table
This is an incomplete list but should provide an idea of my thinking. A list of things to be mounted on the trailer is (currently):
- Bobcat 225
- Oxy acetylene setup
- Air compressor
- Tool Boxes, I anticipate 3-4
One thing I started doing years ago was I converted many of my vices, etc to a mounting system of using standard 2" receiver sized square pipe for mounting. I will incorporate that system in this trailer to be able to just move those pieces of equipment right over for when I need them.
The first area of investigation I'm embarking on is the suspension. As I intend to eliminate the original wheel well space, I need to see if I can restrict the travel of the suspension so the wheels won't hit the bottom of the flat bed. Also, conversely, I might need to pinch the suspension while the trailer is in the table mode to not have the wheels dragging the ground and interfering with the casters. If anyone has any ideas about the suspension or any other suggestions, please fire away. Some might argue that I may be going way too far with what is necessary, but, a) welcome to my world ;-) and b) part of this is to further hone my build skills. I've attached a couple of pictures. One is of the trailer as it currently stands and the other is a first cut at laying out the equipment on the proposed bed with the two wooden blocks indicating where the back corners would be.
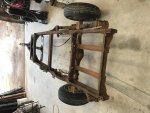
- Leave a fairly large area on the back free for use as a welding table. The height seems very good but will change as the design proceeds.
- Build legs on large casters at the 4 corners to make it a table. The trailer wheels to be off the ground in this configuration.
- Transform the tongue to make it removable so it would truly be a table
This is an incomplete list but should provide an idea of my thinking. A list of things to be mounted on the trailer is (currently):
- Bobcat 225
- Oxy acetylene setup
- Air compressor
- Tool Boxes, I anticipate 3-4
One thing I started doing years ago was I converted many of my vices, etc to a mounting system of using standard 2" receiver sized square pipe for mounting. I will incorporate that system in this trailer to be able to just move those pieces of equipment right over for when I need them.
The first area of investigation I'm embarking on is the suspension. As I intend to eliminate the original wheel well space, I need to see if I can restrict the travel of the suspension so the wheels won't hit the bottom of the flat bed. Also, conversely, I might need to pinch the suspension while the trailer is in the table mode to not have the wheels dragging the ground and interfering with the casters. If anyone has any ideas about the suspension or any other suggestions, please fire away. Some might argue that I may be going way too far with what is necessary, but, a) welcome to my world ;-) and b) part of this is to further hone my build skills. I've attached a couple of pictures. One is of the trailer as it currently stands and the other is a first cut at laying out the equipment on the proposed bed with the two wooden blocks indicating where the back corners would be.
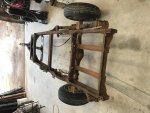