California
Well-known member
Maybe describing my projects can encourage someone who is trying to make up their mind about getting into welding at the amateur level.
I've mentioned in other threads that I'm an amateur, welding as needed for farm repairs and minor fabrication. Here's one of my earliest repairs. It more than paid for the $50 I paid for my first welder.
The Wards Powr-Kraft AC-230 stick welder is probably 50 years old by now. Specs similar to a Tombstone. Got it from an estate sale. I was told Gramps played with it for a year then it just sat for decades. After blowing the dust out and oiling the fan it works same as it did new.
My garage door in town came down on something crooked, and tore the hinge pin out of the arm. I took the components out to the ranch, straightened the bent arm, and welded the pin back in with the torn area beefed up.
As far as I can remember this was my first practical application of this big stick welder. Compared to what it would have cost for a garage door company to fix this, I saved several times more than I paid for the welder.
A pro welder's work would look more refined than this but the hinge is solid, it's been in use since 2007 without issues. I'm pleased with what I can do with this welder. I still have it.
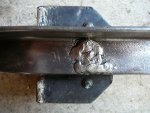
I've mentioned in other threads that I'm an amateur, welding as needed for farm repairs and minor fabrication. Here's one of my earliest repairs. It more than paid for the $50 I paid for my first welder.
The Wards Powr-Kraft AC-230 stick welder is probably 50 years old by now. Specs similar to a Tombstone. Got it from an estate sale. I was told Gramps played with it for a year then it just sat for decades. After blowing the dust out and oiling the fan it works same as it did new.
My garage door in town came down on something crooked, and tore the hinge pin out of the arm. I took the components out to the ranch, straightened the bent arm, and welded the pin back in with the torn area beefed up.
As far as I can remember this was my first practical application of this big stick welder. Compared to what it would have cost for a garage door company to fix this, I saved several times more than I paid for the welder.
A pro welder's work would look more refined than this but the hinge is solid, it's been in use since 2007 without issues. I'm pleased with what I can do with this welder. I still have it.
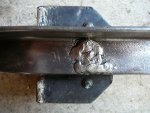