JWeir
Member
So I pulled my dipper cylinder off my Case 580K with my engine lift and brought back to my shop.
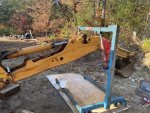
I knew I needed a way to secure the cylinder to my bench so I could unscrew the gland nut with a spanner wrench. I started by cutting an 8" piece off some 1 1/8" diameter rod I had and turning down to 1".
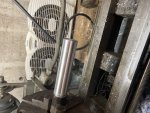
Then I turned some aluminum to 2" to fit inside the end of the cylinder and drilled the inside to 1" to fit over the steel rod.
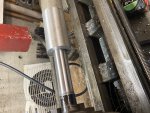
Then I welded the steel rod to a 10 x 12 piece of 3/8" plate.
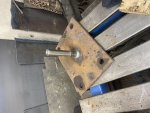
This was clamped to the bench to hold the cylinder.
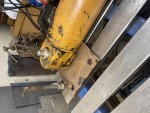
I wanted to add some more support to resist the twisting (I used a 6' bar on a 3/4" drive ratchet to loosen the gland nut). So I cut some 2" square tube legs I welded to the plate and some 2 1/4" upper supports that slide over the legs. I drilled a 1" hole in a 3/8" x 6" plate and welded that to the upper supports. Disregard the old welds on the inside of the upper supports (recycled stock).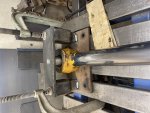
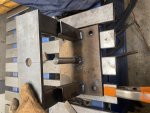
It held a lot of pressure. I had a 10' bar on a 36" pipe wrench on a 2 3/16" socket trying to loosen the piston bolt.
Oh, does anybody know how to fix these pictures so they are not rotated? They look fine on my phone and computer, but not posted here.
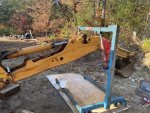
I knew I needed a way to secure the cylinder to my bench so I could unscrew the gland nut with a spanner wrench. I started by cutting an 8" piece off some 1 1/8" diameter rod I had and turning down to 1".
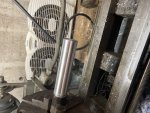
Then I turned some aluminum to 2" to fit inside the end of the cylinder and drilled the inside to 1" to fit over the steel rod.
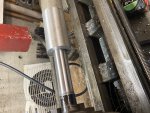
Then I welded the steel rod to a 10 x 12 piece of 3/8" plate.
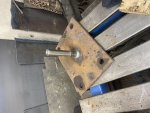
This was clamped to the bench to hold the cylinder.
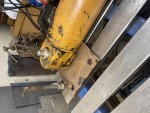
I wanted to add some more support to resist the twisting (I used a 6' bar on a 3/4" drive ratchet to loosen the gland nut). So I cut some 2" square tube legs I welded to the plate and some 2 1/4" upper supports that slide over the legs. I drilled a 1" hole in a 3/8" x 6" plate and welded that to the upper supports. Disregard the old welds on the inside of the upper supports (recycled stock).
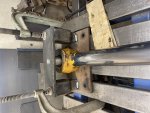
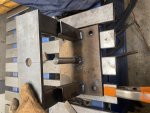
It held a lot of pressure. I had a 10' bar on a 36" pipe wrench on a 2 3/16" socket trying to loosen the piston bolt.
Oh, does anybody know how to fix these pictures so they are not rotated? They look fine on my phone and computer, but not posted here.