CB
Active member
- Messages
- 30
- Good Post Points
- 51
Sometimes, I need flat plate, but not enough flat plate to warrant a trip to the steel yard... and the rape of the wallet that comes along with it... even for scrap steel.
So stitching together flat bar drops of excess material left over from other projects has been a way to create "shapes" of plate.
And it's a lot easier to cross cut a stick of flat bar than it is to pierce cut flat plate. Whether the piercing is manual OA or plasma, or CNC plasma or water jet, a dry cut saw set at miter angle across a 2" flat bar is still faster and cheaper for small projects.
Sometimes, I have a cutoff length of flat bar that isn't long enough, so I'm stitching two drops together to make one longer length.
In all these cases, it still the still the same ol grind... double bevel grind leaving a thin root land, and filling from both sides in an alternate pattern, after fixturing for distortion control.
This project thread isn't about the welding... it's about the same old grind.
Like everything, most of the work is in the preparation.
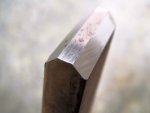
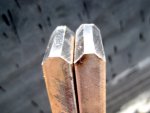
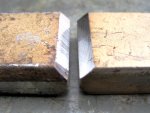
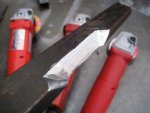
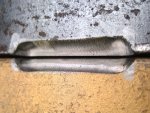
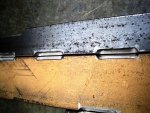
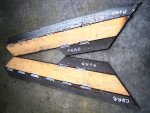
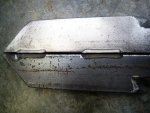
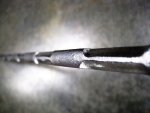
So stitching together flat bar drops of excess material left over from other projects has been a way to create "shapes" of plate.
And it's a lot easier to cross cut a stick of flat bar than it is to pierce cut flat plate. Whether the piercing is manual OA or plasma, or CNC plasma or water jet, a dry cut saw set at miter angle across a 2" flat bar is still faster and cheaper for small projects.
Sometimes, I have a cutoff length of flat bar that isn't long enough, so I'm stitching two drops together to make one longer length.
In all these cases, it still the still the same ol grind... double bevel grind leaving a thin root land, and filling from both sides in an alternate pattern, after fixturing for distortion control.
This project thread isn't about the welding... it's about the same old grind.
Like everything, most of the work is in the preparation.
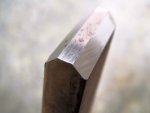
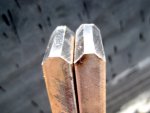
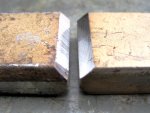
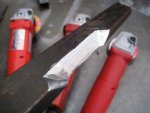
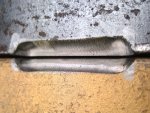
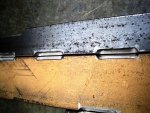
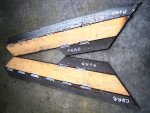
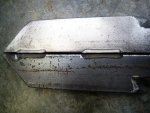
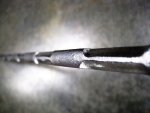